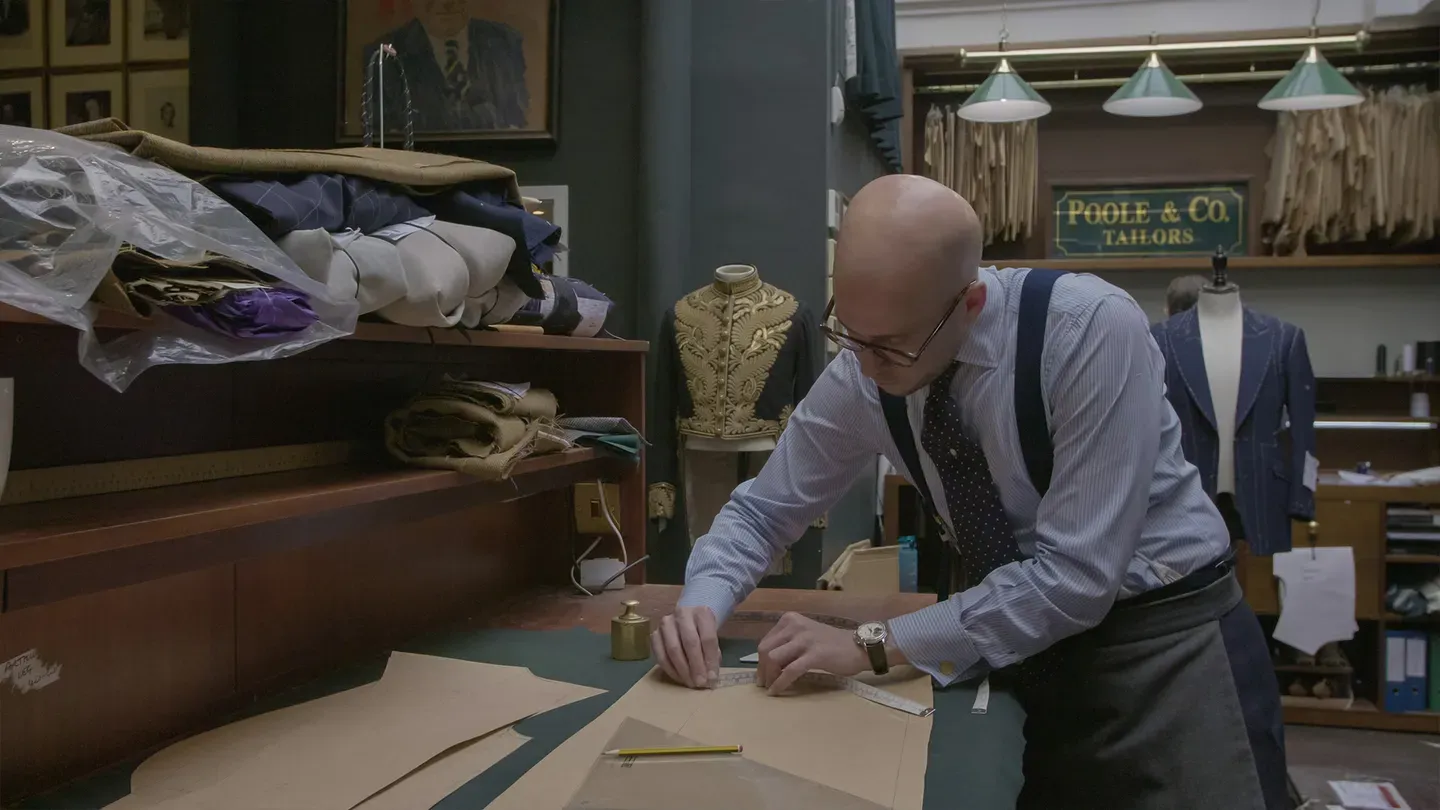
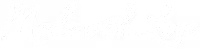
England Made With Love
Special | 57m 52sVideo has Closed Captions
Explore artisan craftsmanship and treasures in one of the world’s most beautiful places.
Explore artisan craftsmanship and hidden treasures in one of the world’s most beautiful countries. Meet the talented and dedicated watchmakers, weavers, bookbinders and roof thatchers who teach hands-on skills to the next generation of apprentices and stay true to the artistry that shaped their lives decades ago.
Problems playing video? | Closed Captioning Feedback
Problems playing video? | Closed Captioning Feedback
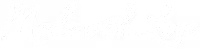
England Made With Love
Special | 57m 52sVideo has Closed Captions
Explore artisan craftsmanship and hidden treasures in one of the world’s most beautiful countries. Meet the talented and dedicated watchmakers, weavers, bookbinders and roof thatchers who teach hands-on skills to the next generation of apprentices and stay true to the artistry that shaped their lives decades ago.
Problems playing video? | Closed Captioning Feedback
How to Watch Made With Love
Made With Love is available to stream on pbs.org and the free PBS App, available on iPhone, Apple TV, Android TV, Android smartphones, Amazon Fire TV, Amazon Fire Tablet, Roku, Samsung Smart TV, and Vizio.
Buy Now
Narrator: England.
From its ancient villages to its bustling cities, this imperial island is rooted in tradition, a place where creativity and vision can find fertile ground.
Man: The UK as a whole really does value and respect craftspeople.
♪ Man: We're surrounded by the ocean, and we've got the whole Atlantic.
Your imagination can take it where you want it to.
Narrator: For thousands of years, this epic landscape has inspired anyone with a sense of wonder, passion, and vision.
You got to be passionate about it.
Otherwise, you know, what's the point?
Narrator: That love of creation has helped produce the clothes, foods, accessories, and more that could only be made here in this land of royal discovery and imagination.
♪ ♪ London--one of the most iconic cities in the world, founded by the Romans in 50 A.D., it's a global power center for finance, politics, and fashion.
They come in all shapes and sizes.
Some are understated, while others are bold and vibrant.
Whatever their style, they're an utterly English accessory.
Man: We've always had a tradition of hat making in this country.
I actually would say that England is the hat capital of the world.
Narrator: English hats have had a long history on the world stage-- from Charlie Chaplin to Queen Elizabeth.
Bennett: We've always had a really good royal family who have always worn hats.
The Queen that's just passed was a great hat wearer, and I think that filters down into real life.
I am Ian Bennett, and I am a milliner from London, England.
Narrator: Ian is not your average milliner.
He has made thousands of unique hats.
This hat I absolutely loved.
In terms of millinery, it doesn't come more special than this one.
Narrator: Today, Ian will be making a bespoke hat for Kim, one of his regular clients.
You bought your outfit.
Yes, a lovely pink.
Fabulous.
Let's have a look.
Narrator: He'll need to dye the hat to match the color of her outfit-- in this case, hot pink.
Here we are.
Narrator: He starts with an ivory-colored piece of fabric called sinamay, which he preps in a bath of vinegar.
This always makes me want to eat fish and chips, the smell of vinegar.
It sort of breaks the seal on the fiber so the fibers can take on a new color and become porous.
Narrator: Then he puts the fabric into the dye.
♪ It can take anywhere from 45 minutes to more than 3 hours to get the right shade.
Bennett: It is getting dark outside, and everyone else has a life, and I'm still stood here dyeing pink.
Yup.
That's about right.
Ha ha!
Narrator: Ian dyes 3 piece of fabric to make the crown of the hat, then paints them with a stiffener.
Bennett, voice-over: Basically, the stiffener acts like a glue, so I would do each of these layers.
♪ Narrator: When the fabric is dry, Ian stretches it, sprays it with water to add flexibility, and then blocks it.
Bennett: You lay all these on, line the weave up like that, so this is why I tell my mum I eat all the pies, because I need a tummy to be able to lean on the table so I can block hats with.
Ha ha ha!
♪ It's difficult because what you're trying to do is, you're trying to make a flat, woven fabric suddenly become 3-dimensional, so you basically got to use sheer brute force.
Narrator: Next, he wraps a blocking cord around the hat to pull it tighter and leaves it to dry overnight.
Then he works on the brim of the hat.
Bennett: When you take this off the block, it would look something like this, so you cut like this along the bottom edge of your block.
This would then go over the top of there... so the two pieces would go together so it would sit like that.
Narrator: After a fitting with a customer, the two pieces of the hat are sewn together.
Then it's time to work on the trim.
Bennett, voice-over: We're actually gonna do what I call my signature bow.
♪ Narrator: When the bow is folded, Ian stitches it onto the hat, and at last, his work is done.
The new hat is ready for Kim to wear.
Bennett: I do love seeing a hat on somebody.
Kim, voice-over: It's fabulous, but then, I always know it'll be fabulous.
Bennett, voice-over: It's one thing to make all this stuff, but when someone buys a hat and makes it their own, I love it.
It's what millinery's all about.
Narrator: What you wear can say a lot about what you do and who you are.
That's why for more than 200 years, Savile Row has been London's premiere destination for stylish, custom-made suits, and, as locals know, the place to go is Henry Poole.
Everyone from Ulysses S. Grant to Frank Lloyd Wright have had their suits made here.
They still dress some of the most influential people in the world, and it all goes back to Henry Poole himself.
Man: He was really a sort of a socialite character, very much sort of enjoyed making clothes, and that's how business started.
Narrator: In the mid 19th century, Henry Poole's customer list was a who's who of European aristocracy, from Napoleon III to England's royal family.
Poole also created a signature look in men's fashion-- the dinner suit.
The jacket soon caught on at a club in Tuxedo Park, New York, and got a new name--the tuxedo.
Man: We still call it the dinner suit here in the UK, but indeed the Americas made it known as a tuxedo, so two different names but the same garment.
Narrator: 7 generations later, this is still a family business.
My name is Simon Cundey.
I'm a tailor, managing director here at Henry Poole, Savile Row in London.
Narrator: At Henry Poole, every one of their signature suits is carefully designed to fit the customer.
♪ Cundey, voice-over: You have your suit made here from start to finish, and that's something which is very special, which customers love.
Narrator: The process starts with a highly-trained cutter, who takes 37 different measurements.
8 3/8.
Will you raise your arm please, sir, and bend at the elbow?
Narrator: When all the measurements are made, the cutter creates a personalized paper pattern for the suit.
Precision is key.
The cleaner you work, the cleaner the job will be at the end of the day.
♪ Narrator: The paper pattern is laid out over the fabric and traced with chalk.
♪ Thorne: We use this to mark the job so it doesn't damage the cloth.
It does take practice, and it's, I mean, a skill you build up over years.
Narrator: The cloth is cut carefully by hand.
The cutter will leave some extra material at certain seams or inlays so the fit can be adjusted over time.
Cundey, voice-over: With a Henry Poole suit, it's one of those sort of things where you buy and you can wear for years to come.
Narrator: The tailor assembles the pieces of fabric as well as attaching sleeves and adding pockets.
Then it's time for the first fitting, where the tailor looks at the suit's overall fit.
See how it's sitting through the shoulders?
We've got a little bit of looseness here, so you ideally want to get it just sitting naturally across the shoulders, so I'm gonna just widen the shoulders a fraction.
Thorne, voice-over: Our job is to find faults, so there'll always be something that we want to improve on.
We're trying to get as close to perfection as we can.
Narrator: Over the course of 3 months, each customer goes through a total of 3 different fittings.
The tailors make small changes each time until finally... What do you think?
It looks beautiful.
Might keep it on for the rest of the day.
Narrator: When a suit is done, notes are kept on file for any future orders.
That kind of strict recordkeeping goes all the way back to the ledgers kept by Henry Poole himself.
Cundey: We're looking around the 1890s.
If I go to page 51 here, the great, legendary J.P. Morgan, of course, from Morgan Stanley.
♪ Narrator: Poole has also dressed 5 British prime ministers, including Winston Churchill.
Cundey: He came to us at the young age of 36, pages and pages of clothes with him.
Narrator: Henry Poole still offers a suit just like one made for Churchill using the very same fabric.
Cundey: This is indeed his flannel chalk stripe he wore in the photograph of him with a Tommy gun and the Coke hat.
He would've worn it with his polka dot tie, which, of course, is very famed for him, as well, so people today can still enjoy those fabrics and tell a story for what they're wearing.
♪ Narrator: For Simon, there's no greater joy than seeing people wear Henry Poole suits out into the world.
The best part is when that customer gets complimented at the airport or complimented at a dinner and said how good that suit looks on you.
That comes back to us, and then we feel our job is done.
♪ Narrator: In a big city like London, what many craftspeople are selling is style, but out in the country, creation can be a more practical matter.
♪ Northeast of London along the coastline is the county of Suffolk.
Suffolk is known for its flatlands and marshes along with its fields of long straw and tall grasses.
For thousands of years, locals used to gather these and weave them together to cover their houses, a process known as thatching.
Today, tens of thousands of buildings across England still have thatched roofs, and a small group of English experts are helping to rebuild and care for them.
I'm Nick Walker.
I'm a master thatcher in Suffolk, England.
Narrator: Nick has been making thatched roofs for 20 years.
Today, he's training the next generation of thatchers.
He starts by showing them the most common material used for thatched roofs--reed.
Walker: The main surface area that you'll see on a roof is reed.
Because it's hollow inside, it traps air, and that makes for great insulation.
♪ The other beautiful thing about it is that you can shape it as you want to.
The roof not only performs really well, but it looks beautiful, as well.
♪ Narrator: He also uses pieces of hazel wood, which gets split in half and then twisted.
These will form the pegs, known as spars or broaches, that hold down the bundles of straw reeds at the top of the roof.
Walker: In at the top.
Boy: Mm-hmm.
Down the grain.
♪ Why do you make it look so easy?
Well, I make it look easy because I put 20 years of experience into it, and maybe about 20 years' time, you're gonna make it look just as easy, as well.
Once they're all made up, what we'll do is, we'll twist them like that and make kind of hazel peg, and you do that because it doesn't break the fibers of the wood.
It remains intact, and then this will get driven deep into the straw, and it pins it down.
It holds this incredibly tight.
Should we split some more?
Narrator: Traditionally, people train for many years before they become a master thatcher.
Nick's sons are getting an early start.
OK.
I think this will be a good one, OK, so you can sometimes tell by the sound how well it-- That's it.
Listen to that, lovely.
That's going right down the middle.
Splitting it in between, I like the sound of it.
It's really satisfying then when it breaks.
Yeah.
That's great.
It is, isn't it?
Beautiful.
You've done that one really well.
That's a beauty, so we'll hand that one to your brother and see if he can sharpen it up, and then we've got the little production line going, and I can sit back and retire pretty much now, I can't I?
No.
I just like the way that it's really satisfying when you go like that and a piece of wood just chips off and it goes really smoothly.
The boys are doing well.
This is a skill which takes a long time to master, and, like many worthy skills, it doesn't come easily.
It doesn't come overnight.
Narrator: Now Nick and his sons head to the roof to help shore it up.
First, they put some new bundles of reed into place.
That's great.
Thank you, Rowan.
♪ What I'm doing here is, I'm placing the bundles of reed into position, and I'm using the leggett to dress them to an even, consistent pitch.
♪ This is how you make a thatched roof.
Narrator: Straw is placed over the reed, then driven into place by the hazel pegs, or spars.
So these are the broaches we were making up earlier, and they're just driven in nice and tight.
They'll hold that in position there.
Narrator: Those spars help secure the bundles of straw to the ridge, which protect the main body of the roof from wind, snow, and rain.
Each layer is held by the broaches, and then there's a surface layer of longer ones and crisscrosses.
It's a decorative pattern, but it's a functional pattern.
It's there because it works.
Narrator: Every thatched roof is made of thousands of bundles of reed.
Walker, voice-over: You use a phenomenal amount of wood and straw and reed in a roof.
That's why they work, because you've got so much packed in there so tightly, that's gonna give it its lifespan.
Narrator: With expert installation and regular maintenance, a thatched roof can last as long as 60 years.
Parts of these roofs will change color over time because of weather and what they're made of.
Walker: People who live under a thatched roof, they have a relationship with their roof.
Most of the roofs I make will outlast me.
Perhaps if my sons wanted to follow into this line of work, they might be rethatching roofs which I've worked on, so really, just you're keeping the flame alive.
You're passing it on to the next generation.
♪ Narrator: Afternoon tea.
It's the quintessential English meal, served with finger sandwiches and scones.
Although tea goes back 5,000 years in China, it only came to England in the mid 17th century.
♪ The English thirst for tea is as strong as ever.
Most of us here drink it every day.
Of course, all those tea drinkers need something to serve it in-- namely, a teapot.
Here at Carters of Suffolk, they've been making teapots for almost 50 years.
They are known around the United Kingdom and the world for designs that range from whimsical to historical.
Man: We are virtually the last company that make handmade ceramic novelty teapots in the whole of the country.
The thing that's unique about them is the fact that they're all handmade, they're all hand-painted, and they're all decorated beautifully.
Narrator: The first ceramic teapots were made over 300 years ago.
Here at Carters of Suffolk, they still use the same techniques as they did back then.
Gillam, voice-over: It's all about manual dexterity and attention to detail and being able to follow through a process.
Narrator: Today, they are making one of their bestsellers-- a teapot designed to look like a stack of Jane Austen books.
They start by pouring a mixture of clay and water into a mold.
♪ After the clay hardens for an hour or two, the mold is broken open.
♪ Turned out quite good, actually.
♪ I'm just cleaning up the rough seams I've just taken off, really.
I'm just making them nice and smooth.
♪ Narrator: The molded teapot is left out to dry for the next 24 to 48 hours.
Then it's painted by hand.
Woman: I'm putting the first coat of underglaze on, and it's a thick enough coat that brings out a nice color when it's glazed.
Narrator: Although the work can be painstaking, it's also very rewarding.
Bridges, voice-over: I like it because it's unique.
It's different.
It's just a lovely job to have.
Otherwise, I wouldn't have been here 30 years.
Narrator: After the teapot is painted, it goes into the kiln to be fired.
Gillam: It's fired at 1,200 degrees.
It takes 12 hours from when you switch the machine on till it gets up to temperature and then another 12 hours to cool down, so you've got 24-hour process time.
Once it comes out there, we then start to put on what I call embellishments-- the decals, the platinum, the gold.
Narrator: The pot goes into the kiln once more to finish it off, and then it's ready for tea time.
♪ Bridges: Makes you happy, and it makes you proud of what you do because we work hard on what we do, so we put a lot of love, a lot of effort, everything into it.
Gillam, voice-over: We make absolutely exquisite items.
I think everyone that gets one appreciates the quality that these are made to.
Narrator: Somerset sits in Southwestern England.
It's a place that mixes natural wonders with manmade beauty, as one can see in its largest city--Bath.
♪ Bath has served as the muse for some legendary authors.
One-time resident Jane Austen famously wrote two novels set in Bath.
Mary Shelley penned much of "Frankenstein" here, and frequent visitor Charles Dickens used the area's namesake baths as inspiration.
Man: So we've got a long, long literary history.
Narrator: That history extends into the modern era, thanks in part to one family's deep love of books.
Man: Great-grandfather, he actually trained as a bookbinder and realized he was quite good at it, so he started his own book bindery, and he also started a bookshop at the same time, and it's his name that's above the door here.
Narrator: Over a hundred years and 4 generations later, that passion for books lives on.
Man: I've always loved books.
I read them when I was young.
I started collecting them when I was a certain age, and I have a house full of books.
I'm Edward Bayntun Coward.
I'm the owner of the George Bayntun Book Bindery in Bath in England.
Narrator: Edward and his team give new life to old books.
They've restored everything from first editions of "Lord of the Rings" to one of the most influential books of all-- the King James Bible.
The process is painstaking.
It takes at least 3 months and can be as long as a year.
Coward, voice-over: We have to be patient because the process involves about a hundred different stages.
Every page, every sheet is taken apart and examined, and it needs be restored and cleaned, and then the process of rebuilding the book starts.
Everything we do is done by hand.
Narrator: Bookbinding is both for looks and for protection.
It helps preserve the pages within, but no binding lasts forever.
Coward: Someone comes to us and says, "This is my book.
It's a favorite book.
I just want you to rebind it."
Narrator: Today, Edward and his team will be restoring a first edition of a classic 20th-century novel-- "Winnie the Pooh."
Coward: The Winnie the Pooh books, first one was in 1924, and they have just been all-time bestsellers.
When first published, they were a limited number because it wasn't well-known, so the first book is rare.
Narrator: The process starts by taking off the cover and pulling the book.
So what I'm doing is taking it to pieces.
Once it's been taken completely to pieces, you've got flat sheets that you can then work on to repair or to clean.
♪ Narrator: As the pages are reassembled, the spine gets flattened.
In order to round the spine out again, the pages are clamped into a backing machine from the Victorian era.
Man, voice-over: I'm just gonna bring this roller, this heavy roller, onto the back of the book, and I'm gonna move it across in the cam of the spine, the shape of the spine, and it'll crisp everything up.
♪ Just releasing the book from the star backer, also known as a jobbing backer... ♪ and it facilitates us creating the rounded spine and shoulders of the traditional form of a book.
Narrator: After the pages are trimmed, they are painted with an adhesive called glair.
This allows the bookbinders to attach gold leaf.
♪ Gold gives the book an elegant look and helps protect the pages from moisture and dust.
Next, a leather skin is chosen and cut to size with a paring knife.
Coward, voice-over: The leather, which has to be all pared by hand, is used to cover the book, and then it goes to the far end of the book bindery, where we have someone called a finisher, which is the person who finishes it all.
Narrator: The finisher uses a variety of heated tools to letter and decorate the book.
They've got more than 15,000 to choose from, all made by hand.
Coward: voice-over: We have got the largest collection of finishing tools in the world.
♪ Narrator: When the binding is finished, the book is ready to go back on the shelf where it belongs.
Coward: The most satisfying part of the job is seeing a book which you know is an important book.
It's a book which has a history, and we put it all back together again, and we make it good for, I could say, centuries to come.
Narrator: North of Somerset is Staffordshire, a landlocked county in the West Midlands.
First settled in the sixth century, parts of this region may look as though time has stood still, but, of course, that's just an illusion.
♪ [Bells tolling] Clocks and watches-- without them, we wouldn't know when to get up, meet a friend, or leave the office.
While the Swiss became known for their early watches, the English soon closed the gap.
By 1800, Britain was making almost half of all watches worldwide by hand.
Today, most watches are mass-produced.
Luckily, there are still a few English experts who can help us mark our journey from past to future by making these key tools of timekeeping.
So those two, just trying to follow it up with this little adjustment.
OK. Yeah.
I'm Craig Struthers.
And I'm Rebecca Struthers.
We're watchmakers.
From Leek in England.
Narrator: Rebecca and Craig first met in art school, where they learned about far more than painting and sculpture.
They discovered the singular craft of watchmaking.
At the time, I didn't know it was a career, but I set foot in the workshop, and I was just like, "Yes.
This is what I want to do with my life."
Narrator: Together, Rebecca and Craig have spent the last decade studying, repairing, and recreating vintage and antique watches.
[Ticking] Craig: We chose to make a manual-wind wristwatch based on a very basic pocket watch from around 1890, so we make brand-new watches that are already 100 years old, if that makes sense.
Rebecca: Every watch is handmade to order, so everything, to an extent, is unique.
Narrator: As they start building a new watch, they use the same machines they first opened their business with, many of them 100-year-old hand-me-downs.
Rebecca: And they all have names.
They're like an inanimate workforce, aren't they, our team.
Craig: So basically, even though it's just me and Rebecca, we do talk to the machines.
They have characters.
Yeah.
Craig, voice-over: This is Barney, our case-making lathe.
The way we do case making is soldiering up rings of gold or silver, and then we glue them onto boxwood, and then we can put them in the lathe and then turn the different steps for the movement to sit in.
Narrator: The watch case is the housing that holds and protects the inner workings of these classically-designed watches.
Inside, every watch is powered by a series of large and small gears, each of which is made by hand.
It can take up to a year to finish an entire watch, with Rebecca and Craig working together every step of the way.
Craig: I think the good thing about me and Rebecca is, we've got opposite skill sets.
Yeah, and we really get on.
You do a lot of the fine hand turnings.
I do a lot of the kind of the engineering design side of things.
Individually, we're OK watchmakers, but without one or the other, I think it wouldn't work as well, definitely.
Yeah.
Narrator: That sense of collaboration keeps the gears turning smoothly, as does their shared passion for watchmaking.
I love my job.
I love the history of it.
I just think the most beautiful things have already been made, so getting to work with the old stuff as well as designing and making new stuff is just the perfect combination.
Narrator: Smack in the middle of England sits Northamptonshire, an area so rural, it has no major cities, just one large town-- Northampton.
In the 19th century, Northampton became known for its massive footprint in the shoemaking industry.
Woman: Northampton traditionally was known for shoemaking because of all of the forests and land, so they used to tan all of the leather here as well as make the shoes.
It was known as the sort of shoe capital for menswear in the UK.
Narrator: During the First World War, this area supplied more than 2/3 of the 70 million pairs of shoes used by Allied soldiers, but times have changed.
There once was roughly 170 factories in the county.
Now there are 11 left.
Narrator: One of the area's surviving shoemakers goes all the way back to the early days of local shoemaking.
It's a company called Tricker's.
Williamson: We are a family-owned business still functioning in the heart of Northampton in an old, 3-story, Victorian factory.
A Tricker's shoe or boot, they're a really sturdy construction, so the way that they're made allows them to be repaired.
My name is Adele Williamson.
I am a master bespoke shoemaker based in Northampton, England.
I've always had a passion for creativity and design.
I never thought I'd be a shoemaker.
I didn't realize the job really existed anymore.
Narrator: During college, Adele had a chance to study footwear design and work as an intern at a shoe factory.
Williamson, voice-over: It's a trade that takes a long time to learn, and I realized this craft was something I really had a passion for, I really wanted to focus on.
Narrator: At first, she felt like she was trying to make her way in a man's world.
People just followed in footsteps of others, and it's just predominantly always been males that have done this job, so when I started, I maybe created a bit of a stir, but it is open to anybody who would like to give it a go.
Here at Tricker's, each bespoke shoe starts with a last, a wooden mold made in the size and shape of the customer's foot.
I would meet the customer, measure their feet, and this would then be turned into a wooden form based on the style of shoe that is desired.
Narrator: Then they chose the right material, working with the best European leather they can find.
Williamson: So this is our leather stock room.
It's where we keep all of our raw materials.
♪ Narrator: Then it's off to the clicking room, where templates are used to cut out pieces of leather.
Williamson: Each time the knife perforates the leather, it makes a clicking sound, which is where the name clicking came from.
Each piece will be cut out, and the leather will then be put into different piles of components, ready to be prepared for the next stage.
Narrator: They also punch holes into the toes of the shoes to give them their distinct Tricker's style.
♪ Then the pieces are taken to the closing room.
This is where all of the components get stitched together.
This is one of our classics.
It's a Stow boot in the acorn leather.
As you can see here, they're assembled in this room, and the next stage will be to stitch this in here and this in here.
Narrator: By stitching together the pieces of leather, they create the upper, which is every part of the shoe that's above the sole.
Williamson: So we have the upper.
We can then stretch this over the customer's wooden form, and that's how then the shoes starts to take its shape.
♪ Narrator: Next, they prepare the insole, which will be attached to the upper.
Williamson: This machine creates this groove around the edge of the insole.
It is very old.
There's only, I think, two remaining in the county, this being one of them, dates back to late 1800s.
♪ Narrator: Finally, they attach the upper to the insole.
They use waxed threads, which they make themselves, to stitch the pieces together through something called a welt, a strip of leather that gives the shoe its structure.
It's quite a strenuous job, stitching welts in.
You have to completely pull your arms out every single stitch, and, as you can see, in some styles, they can have, you know, 70 to 100 stitches per foot.
Narrator: The last step is adding the heel, and the shoe is done... ♪ but the whole process takes a lot longer than walking into the shoe store.
♪ Williamson: So from meeting the client to the finished article, it's 12 to 18 months.
♪ Narrator: Learning to make these handmade shoes has put Adele on a path she hopes to walk for many years to come.
Williamson, voice-over: I definitely feel the sense of responsibility to continue the craft.
I really, really enjoy what I do, and I think the versatility of meeting clients and making the shoes, for me, it feeds everything I need.
♪ Narrator: In the North of England lies Greater Manchester, which encompasses what was once the beating heart of the Industrial Revolution.
The textile industry traces its roots here all the way back to 1572.
The French Huguenots, known as skilled weavers, fled France for England to escape religious persecution.
One of those families in exile was the Mallalieus.
They brought their textile know-how to the small village of Delph.
In 1863, at the height of the Industrial Revolution, the Mallalieus officially founded their namesake company.
Over 150 years later, it's still here with a name that represents generations of quality weaving.
♪ We use only the best fibers and the best dyes.
♪ Man, voice-over: We are known for tweed.
We design a new collection every year, which we present around the world.
Britain has a look, doesn't it, and I think tweed is part of that look, and we're proud to carry on the tradition.
Narrator: Today, Mallalieus is one of a handful of British fabric makers that produces everything they make, such as wool blankets, here on site.
The process starts with the wool itself, which they source from all over the world.
It feels quite soft, so it'll do the product that we want it for.
Narrator: Then heat and dye are added to create different shades of wool.
Temperature control is key.
We dye the wool at the maximum of 90 degrees Celsius.
You don't take it up to boil because the fiber would deteriorate.
Narrator: Then the wool goes into a teasing machine, where it gets blended.
Gledhill, voice-over: When you make a blend, you pass it through a number of times.
Then you fan it to spread it, and in spreading it, you mix it, so if you're using different fibers to make a blend, then it spreads them all together and evens it, so you pass it on 3 occasions through there, and you finally put the lubricant on prior to carding.
Narrator: During carding, the fibers are separated and combed out.
Then the wool is spun to form spools of yarn.
After that, the wool is ready for warping.
Long threads of yarn are stretched lengthwise on a loom.
We warp the fabric, first of all.
That goes onto beams, so any yarn in the wrong place will create wrong designs.
♪ Any broken ends have to be corrected.
They have to be fault-free at this stage.
Narrator: At last, the weaving begins with threads interlaced by 24 looms.
♪ When it's over, each blanket is hand-checked for imperfections.
♪ Then it's off to finishing, where the wool gets a final wash. Walsh: They always say woolen fabric is made in the finishing.
We use the water from the River Tame to get the soft handle we need on our fabrics.
Narrator: More than 400 years after the first wool fabrics were made here, the name Mallalieus still stands for quality and passion.
Gledhill: It's making a good product that people appreciate.
I think it's important that you understand who's buying it, what the sort of level it is.
Gledhill, voice-over: Very proud, actually, that we've created something.
I don't regret for one minute what I've done in my life.
I've enjoyed it and still do.
Narrator: The vistas of Somerset in Southwest England can be a feast for the eyes, but perhaps the best way to experience this area is with your taste buds.
Everyone knows cheddar cheese, brightly-colored and sharp on the tongue, but what few know is that it comes from a place called Cheddar in Somerset, England.
♪ Ha!
How do you describe Cheddar?
It's this lovely, little, rural village.
You know, you've got all the geography.
You've got all the history, you know, beautiful scenery.
Narrator: Cheddar is also known for its network of caves.
According to local legend, a milkmaid left a bucket of milk to cool in one of these caves, then came back to find a pail full of cheese.
In truth, it's not that easy.
It's quite the process.
A little bit of science in there as well.
Narrator: The royal family has long had a taste for cheddar.
In 1170, King Henry II bought more than 10,000 pounds of cheddar.
Woman, voice-over: For a very long time, unless you lived in the local area or you're at the King's court, you could not get cheddar.
Narrator: Almost 1,000 years later, cheddar is as popular as ever.
It's made all around the world.
Doesn't make it all equal, and it's great that people can come here and experience the real thing.
I'm Luke Shepherd.
I'm Emma Hill.
We're cheesemakers.
From Cheddar, England.
Narrator: Today, English-made cheddar is making a comeback.
For Emma and Luke, it all starts with a mixture of locally-farmed milk, water, and rennet, a starter culture.
This blend is cut, then left untouched for about an hour until it sets.
As the mixture is heated, it separates into curds, a solid, and whey, a liquid.
We'll drain off the byproduct, which is the whey, and what we'll be left with is all this curd.
Narrator: When the curds are ready, they drain the whey from the vat, then bring large chunks of curds to the cooling table.
Shepherd, voice-over: When it's on the table, it literally comes together like a solid again, so, then we have to break it all up by hand, cut it into blocks, and then flip them and then stack them.
Narrator: Stacking the curds helps add the texture and flavor that make cheddar cheese unique.
Then the curds are put into molds and lined up in the cheese press, where they're left overnight.
By the next morning, the curds are taken out of the molds, wrapped in cheesecloth, and bathed in hot water to help smooth out their shape.
At this stage, this is no longer just curds-- it's a young cheese, but it still needs to age.
Luckily, Emma and Luke know the perfect spot-- the same caves where people have been aging cheddar for hundreds of years.
The caves stay at 11 degrees Celsius all year long, making this a perfect place for cheese to mature.
Hill, voice-over: You get that little whiff of cheese as you're coming up the slope.
Ah, yeah, that's the cheese up there.
Shepherd, voice-over: It's a natural environment.
It offers a unique flavor to our cheese which is completely different to any of our other flavored cheeses.
Hill, voice-over: There's quite a natural high humidity, so, the cheese isn't gonna dry out as much.
Narrator: That moisture causes mold to grow, adding to the flavor, but too much mold will affect the rind.
Hill, voice-over: So, we just come in here about once a week.
We give them a little bit of a rubdown, give them a little bit of love.
We turn the cheeses as well to make sure they mature evenly.
I picked the heaviest one this time.
Ha ha!
Hill, voice-over: It's always quite nice to just come up here and have a little chat with the cheese if you're having a bit of a bad day, The secrets a cheese could tell you is pretty interesting.
Narrator: After at least 6 months in the cave, the cheddar is aged.
Emma, do you want to grab the 4th of April?
That looks like it's ready to come down.
Narrator: Now it's time to give it a taste.
Mm.
I do like the cave-mature cheese.
Yeah, it's my favorite out of all the cheeses.
It's very complex.
There's a lot going on in there.
Narrator: Making cheese in the birthplace of cheddar is more than just a job-- it's a way to bridge the present and the past.
Hill, voice-over: It's an honor and a privilege to be a part of this.
This is where we live, this is part of our heritage, and this is a dying trade.
We're making this beautiful, proper, traditional cheddar, and it's great to be a part of that.
Because if we don't do it, nobody else is going to.
Narrator: Emma carries on that tradition with a sense of pride-- and passion.
A lot of love, a lot of time goes into this.
You've got to be passionate about it.
Otherwise, you know, what's the point?
♪ Narrator: Sitting on England's southwestern tip, Cornwall may be the most remote corner of this island nation.
♪ It's a peninsula that juts out into the Atlantic with huge swaths of open moorland as well as some 400 beaches.
One local craftsman, known as a woodturner, uses that rugged terrain for raw material as well as inspiration.
Jamie Zennor, voice-over: We've got beautiful countryside, lots of woodland, and we've got coastline, so, loads of places I could potentially find interesting wood.
A piece of wood could have come off a cliff in California and made it across here, or it might have fallen off a cliff two miles down the road.
That mystery is part of the fun of the exploration of that piece of wood.
I'm Jamie, I'm a woodturner from Cornwall, England, and this is Bob.
A woodturner is somebody who turns wood, so, we would sculpt shapes from the wood.
The wood's usually spinning.
That's where the turning comes in.
Narrator: Jamie has made everything from bowls to works of art, and he does it all with resources found close to home.
Zennor, voice-over: The wood I get is all locally sourced.
When I see a good bit, that's like gold dust to me.
Narrator: Jamie first started working with wood as a boy.
Zennor, voice-over: I was taught at school when I was about 12, 13 years old, and never stopped.
Narrator: Today, Jamie is taking a piece of raw cherry wood and turning it into a bowl.
Zennor, voice-over: I cut all the excess off to get it to a rough, round shape, so, I've removed and exposed areas which will give some nice features within the wood.
That's the bits we're looking for, really.
[Whirring] Narrator: Jamie puts on a metal plate so that he can attach it to the lathe.
♪ Then he chooses a chisel and gets to work.
Zennor, voice-over: At the moment when I'm turning the wood, when it's spinning and my chisel's making contact with it, that's meditation to me.
Everything else just ceases to exist and you're in your own little world.
It's mesmerizing.
Narrator: As the wood reveals itself, Jamie notices what's known as spalting.
Zennor, voice-over: Spalting is where the fungus gets into the wood and it starts to leave staining in the timber.
And you get these black lines which just look like someone's gone in with a fine liner, and that's nature doing its art for me.
Narrator: Next, Jamie starts to scoop out what will become the inside of the bowl, revealing the layers within.
♪ Zennor, voice-over: This was the outside of the tree where the bark was, and each scoop, we're going down through into the older part of the tree and unveiling all those different years of grain.
Narrator: As Jamie works, he has to be careful not to drive his chisel too deep.
Zennor, voice-over: The bowl isn't round.
It's got bits missing.
So, if I catch the chisel and it creates a big impact, it can split the wood.
There's an element of intuition.
You can hear the wood, you can hear how it's behaving, you can feel the feedback through the tools, and you know when something's not right.
This is pretty much finished now.
Narrator: When the bowl has taken on the shape he wants, Jamie sands it down.
♪ Then he rubs on an organic hemp oil to finish the wood.
♪ It just brings out all the colors and grain in the wood, and it produces a really good, natural, long-lasting finish.
♪ No chemicals, no additives.
Natural.
We've got some beautiful figure in the wood.
Lovely grain, lovely coloring.
And you can really get a feeling for the age of the tree.
♪ Narrator: For Jamie, taking a piece of wood and helping transform it into something new is like magic--a trick he's happy to perform again and again.
Zennor, voice-over: Unconditionally love my job.
It doesn't feel hard work.
I can be sweating and I'm enjoying myself.
It's not a job.
It's play.
Narrator: Back in London, there are many iconic sites, but perhaps nothing represents England's capital city quite like these--umbrellas.
The earliest ones can be traced back thousands of years, but they didn't take off in England until the early 1800s, when the rise of the middle class led to more leisure time and outdoor activities.
A lot has changed since then, but one thing's stayed the same-- you can still buy an umbrella from the Ince family.
Man, voice-over: The business has been going for 218 years now.
♪ I am Richard Ince, an umbrella manufacturer in East London.
Narrator: Ince is the oldest umbrella maker in the United Kingdom.
Lucky for Richard, the sixth generation of Inces to run this company, it's a product that never goes out of style.
Ince, voice-over: The umbrella for the English, it's almost like a comfort blanket or just a familiar friend.
It's in the DNA to a degree.
Narrator: Umbrellas are usually highly practical, but Richard has made some show-stopping umbrellas for events such as the Super Bowl.
Ince, voice-over: Coldplay played at Super Bowl 50 and we made all the flower umbrellas for their show at halftime.
Inverted umbrellas.
That was quite something.
Narrator: Today, Richard is sticking to a more classic product--the gent's solid stick umbrella.
He starts by measuring the frame to figure out where to cut the holes for the hand and top springs.
♪ Ince, voice-over: This'll keep the umbrella open and which'll keep the umbrella closed.
And we fit a small rubber ring.
It just enables the umbrella to behave itself a bit better in use.
♪ Narrator: Next, Richard attaches a metal skeleton, which will need to open and close smoothly.
Ince, voice-over: So, we're just making sure that everything's in line.
We just micro-adjust it a little bit so everything's going to work properly.
♪ Narrator: Before Richard puts on the canopy, there's one last step-- he slides on the ferrule, the protective tip on top.
♪ So, that's nice and neat.
Narrator: Now it's time to add the fabric.
Ince, voice-over: It's super dense weave, so, it keeps the rain out, but it also has a sun protection factor on it as well.
Nothing too fancy about it, but it just does the job well.
Narrator: Richard sews the fabric into the frame.
Then he secures a metal circle to the canopy to hold all of the pieces of fabric together.
Finally, the distinctive rosette gets sewn on.
It helps protect the user's hand from the metal underneath.
It also makes every Ince umbrella unique.
Ince, voice-over: Just these little touches whereby someone has hand-sewn something just for you on your umbrella.
Narrator: Each one is made with the same level of quality the Ince family has kept up for generations.
Every one of them goes out of here and I'm proud to say they've got my name in them.
That's what keeps me going, is making well-made products that we can be proud of.
♪ Narrator: Globes-- they're works of art that help us see the world by shrinking it down to size.
Many people are fascinated with maps and many people are fascinated with globes.
It's one of the first things you see as a kid.
Narrator: British explorers like Francis Drake, Henry Hudson, and James Cook helped fill in the blank spots during the early days of globe-making.
These globes were traded as gifts among world leaders-- symbols of power that showed who was in control.
Today's globes are more about possibility and sharing the love of travel and knowledge with a new generation.
The thing that inspired me was the great globe makers of the past and seeing how amazing their globes were and thinking, well, if they could do that with the materials available then, I can at least match them.
I'm Peter Bellerby.
I'm a globe maker from North London.
Narrator: At first, Peter Bellerby was just trying to buy a present for his father's 80th birthday--a globe.
Bellerby, voice-over: I went into shops, I went into auction houses, and they were either cheap and plastic or crazy expensive and very delicate.
Narrator: Then Peter had an idea-- he would make a globe himself.
Bellerby, voice-over: So, I thought I had a few months.
It took me two years and all my savings, because globes take a lot of time, patience, and money.
Narrator: By then, Peter realized there might be a demand for handmade globes-- and launched his own company.
Bellerby, voice-over: When I started, I felt I should reach back into the past and do everything in the traditional way.
I then realized modern materials are amazing.
So, you've got to marry the two together.
Narrator: Peter and his team make over 500 globes a year, with each one taking several months to finish.
Bellerby, voice-over: When we're talking with a customer, they'll ask us to add an illustration or maybe an animal.
You can also add on your own little town that you were born in.
Narrator: Next, the globe makers print out what are known as the gores-- panels of map that will form the surface of the globe.
Bellerby, voice-over: We obviously are very rigorous in ensuring that country names and capitals are all as they should be.
Narrator: That same sense of rigor applies to cutting the gores out.
Bellerby, voice-over: So, this is cutting the gore very accurately to one side of the longitude line.
Narrator: Then color is added to the oceans.
Each one gets between 3 and 7 coats of paint.
Woman, voice-over: You have to paint the oceans beforehand because the world is round and if we were to do this after the globe is made, you would get watercolor running all around the sphere, and then the paint wouldn't stay in the oceans anymore.
Narrator: Each globe, known at this stage as the sphere, has slight differences, so, they carefully mark the polar regions and the equator.
Bellerby, voice-over: Obviously it's very easy to find a north pole, but finding the exact opposite position on any sphere becomes more and more difficult.
Narrator: Next, they add glue to the gores and lay them onto the sphere.
The paper is very fragile, and even a small mistake at this stage could mean remaking the entire globe.
Man, voice-over: By the moment we place the first gore, we can immediately tell that something's slightly off.
We'll place it on the equator and just make sure that kind of lines up.
It's very much, once it's on, you kind of need to make sure it's on properly.
Narrator: The gores are put on precisely, and then the globe moves on to the painters.
We'll paint the land and put all the details of mountain ranges and forests and deserts.
It's the world and the Earth, and it kind of inspires you to want to travel and it just looks very beautiful.
I think it's just a very interesting shape to paint over and over again.
Narrator: Finally, the globe's surface is sealed with a resin and a finish so that it's safe to be touched and spun.
Bellerby, voice-over: It's just kind of nice to look at them and see them run just before they go.
We only ever see them complete for a day or two.
Customers see them for the rest of their lives.
Narrator: Although Peter fell into this craft by accident, he doesn't need a globe to see he's on the right path.
Bellerby, voice-over: I totally love my job.
I love every day about it.
I get up in the morning and work for an hour and a half before I come into work and then I'm working here all day, and then I go home and I'm working from home.
I don't need to motivate myself.
It's so much fun.
♪ Narrator: Here in England, where echoes of this nation's noble past lie at every turn, artisans respect that long history while embracing innovation and bringing a sense of love to everything they do.
♪
England Made with Love: Meet More Artisans
Video has Closed Captions
Clip: Special | 7m 4s | Meet more artisans from England Made with Love. (7m 4s)
England Made with Love Preview
Video has Closed Captions
Preview: Special | 30s | Explore artisan craftsmanship and treasures in one of the world’s most beautiful places. (30s)
Providing Support for PBS.org
Learn Moreabout PBS online sponsorshipSupport for PBS provided by: